3D Printing Phoenix transforms digital CAD files into three-dimensional physical solid models. This is accomplished through layer-by-layer fabrication with precision and control.
This technology eliminates redesign cycles when transitioning to production and minimizes financial risk. It also lets businesses obtain market feedback and customer or investor interest quickly.
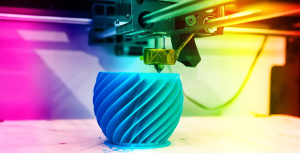
Additionally, 3D printing allows the use of a variety of materials, which opens up a new world of possibilities for creating parts and products. This is especially true for medical applications.
Rapid Prototyping
Rapid prototyping allows teams to test out their ideas and see how they work without spending time building a full-scale production model. This reduces the risk of wasting money and resources on an unsuccessful prototype, and it lets the team know that they have something worth continuing to develop. This process requires teams to be sensitive to the reactions of users, so they can quickly identify what works and doesn’t. It also requires a delicate balance between making the prototype look real enough that users will react to it, and keeping the cost low enough that it’s not expensive to throw it away once it has been tested.
A variety of 3D printing methods can be used for rapid prototyping, depending on the needs of each project. For example, stereolithography (SLA) is a popular technique that creates incredibly detailed models with high precision. This makes it ideal for projects that require an exceptional level of accuracy, such as those in the aerospace or medical industries.
Another common technique is injection molding, which uses the same process as production manufacturing to build a plastic prototype or a finished part. This process allows the designer to use any engineering-grade plastic or liquid silicone rubber (LSR), and it produces strong, accurate parts with smooth surfaces. It is ideal for testing out different materials, color combinations, transparencies, and flexibilities in a single part.
Other popular 3D printing technologies for prototyping include selective laser melting, laminated object manufacturing, digital light processing, and binder jetting. SLM, also called powder-bed fusion, builds prototypes and production parts layer by layer from metals like titanium, aluminum, and stainless steel. LOM additive technology adheres layers of machine-cut paper, plastic, or other material together to fabricate parts, while binder jetting is a fast and inexpensive 3D printing method that utilizes multiple different material powders.
Regardless of which method is chosen, the goal is to produce prototypes quickly and inexpensively, so that designers can make quick revisions to their designs as needed. This process can prevent costly design flaws, speed up production times, and improve overall product quality.
Advanced Materials
The advancements in materials have pushed the uses of 3D printing beyond form and fit models and prototypes to functional parts for testing, as well as end-use production. Advanced materials include polymers, reinforced composites, high-temperature metals and technical ceramics, making them suitable for a variety of applications in industries like healthcare, aerospace, automotive and manufacturing.
While plastic-based filaments and resins remain the most common 3D printer feedstock, engineers are working to improve other, more specialized and long-lasting materials that are more effective for some applications. These advances are also leading to new types of smart materials that have the ability to adapt their shape after being printed.
Aside from material advances, 3D printing has become more effective by reducing errors and improving the precision of the print process. By mastering advanced techniques such as layer height optimization and infill patterning, professionals can achieve the ideal balance of precision, material usage and structural integrity.
For example, in order to increase the tensile strength of a print, annealing is a process that increases the intermolecular bonds of the polymer chains and transforms them into a more crystalline structure. This allows the chains to become stronger without affecting the appearance or properties of the part. This is accomplished by exposing the part to temperature-controlled environment, such as an oven or a heated water bath.
The annealing process can also improve the mechanical properties of a 3D-printed part by increasing its impact resistance and elongation at break. In addition to enhancing the mechanical properties of the part, annealing can help reduce shrinkage and warping.
Specialized printers exist for working with a range of different materials, from concrete to biological matter. These printers are often large and expensive, however, they are capable of producing high-quality products that would be difficult or impossible to manufacture using traditional methods.
Other materials that can be used in 3D printing include flexible polymers, such as thermoplastic elastomers (TPE) and thermoplastic polyurethanes (TPU). These flexible materials have rubber-like qualities, which makes them a great choice for creating soft-touch components or parts that need to bend and compress.
Reduced Costs
While additive manufacturing has many advantages, it can still be a costly process. Fortunately, there are ways to reduce these costs without sacrificing quality or speed. In addition to the initial investment in the 3D printer, labor and energy expenditures can eat into the bottom line. By refining daily operations and making strategic decisions, companies can keep their printing expenses in check.
Choosing the right materials for a specific application can significantly reduce cost. For example, Fused Filament Fabrication (FFF) printers use inexpensive plastics that are easy to replace. However, they also require a lot of power and can waste a lot of material if not operated correctly. For this reason, it’s best to only choose this technology for prototypes and visual models. Alternatively, higher-end printing technologies such as Selective Laser Sintering and Carbon DLS utilize expensive materials that are more durable but require more expertise to operate.
The choice of whether to print in-house or outsource can also affect printing costs. In-house printing can control production and help to lower costs per part over time, but it requires a significant upfront investment and skilled operation. Outsourcing can reduce startup costs and is a great option for low-volume or infrequent needs.
Another way to lower cost is to optimize the design for print. For example, hollowing out a model can reduce overall material usage while maintaining the strength of the part. This is particularly important for processes such as Multi Jet Fusion and Selective Laser Sintering that use powdered materials.
Other ways to reduce printing costs include reducing print size and printing multiple parts at once. For example, GE created a new design for fuel nozzles in their LEAP aircraft engines. These nozzles used to be made from several parts that required assembly, but the company was able to create a single piece that saved them time and money.
Many industries maintain a stockpile of spare parts for frequent and infrequently needed products. However, these spare parts can be costly to store and can increase supply chain costs. 3D printing allows for the production of spare parts on demand, which can reduce inventory costs and streamline the supply chain. This also eliminates the need to ship heavy and fragile parts, which can decrease shipping costs.
Customization
In many cases, the advantage of using 3D printing technology is the ability to customize a product or part to meet specific design preferences and functionality. This has been proven in fields as diverse as fashion, where custom-made jewelry and footwear stand out, automotive, where tailored car parts are revolutionizing automobiles, and the medical world, where customized implants are improving patient outcomes.
Customization is accomplished by using 3D printing to build up layers of a particular material to form a desired shape. The most popular 3D printing process is a material extrusion technique called fused deposition modeling, or FDM. This is a versatile technology that supports many different materials, including thermoplastics such as polylactic acid (PLA), acrylonitrile butadiene styrene (ABS), and thermapol, as well as metals and a wide range of biocompatible plastics. The choice of material determines the physical properties of the final printed object, as well as its cost and ease of printing.
To prepare a model for printing, it is necessary to remove any unnecessary material, and add support structures that will prevent sagging or collapse during the printing process. In some cases, it may also be beneficial to simplify the model’s geometry in order to print it more quickly or to reduce the total build volume.
When the printing is complete, the support structures must be removed, and the surface of the printed object may need to be smoothed or painted. Depending on the print and the material used, this can be a lengthy process. In some cases, additional post-processing steps may be required, such as heat treatment to alter the material’s properties or machining to achieve precise shapes.
While 3D printing is a versatile and effective manufacturing method, it can be tricky to work with for newcomers. The best approach is to start small and learn as you go. Use each printed iteration as an opportunity to make small adjustments and compare the results. Over time, you’ll develop a strong understanding of how to design for 3D printing.
Using 3D printing to test and iterate product concepts trims your design-to-manufacture timeline significantly, and can save you valuable time and money in the long run. For more information about how to make the most of this flexible technology, contact a TWI Industrial Membership representative.